By 2050, the fashion industry is set to use up to 25% of the world’s carbon budget - it’s the world’s second biggest polluter after fossil fuels. While 80 billion pieces of clothing are produced annually, every second, a truckload of used clothes is thrown into landfills or incinerated. This is a colossal waste of resources while toxins and microfibres from polyester and nylon leach into the earth, posing a serious threat to ecosystems, marine life, and human health.
Current polyester and plastic recycling methods mean it can typically only be recycled once due to material breaking down during the recycling process. But that’s now set to change: circular economy startup Ambercycle has developed a groundbreaking solution that makes it possible to repeatedly recycle and reuse polyester in clothing.
As college roommates, Ambercycle co-founders, Shay Sethi and Moby Ahmed, had become obsessed with the idea that they could break through current limitations on polyester textile recycling.
“We started investigating and asked people in the industry, “Why is clothing production this way?” says Sethi. “We found if you ask many questions, you get a lot of responses to the effect of, ‘Oh, that’s just how it is.’ What’s remarkable is that if you keep asking these questions, you find the answers don’t have any valid reason behind them.”
Despite recycling of polyester textiles having been almost non-existent in the clothing industry, Sethi and Ahmed were driven by an insatiable belief that better was possible and that a circular economy was worth fighting for: “We would brainstorm and think about things. In California, we’re told that plastic water bottles are recycled. We found that’s not true for a lot of plastic materials. One day, we were wondering what to do with a bag of old clothes, and we learnt that in clothing, more than 70% of apparel is land-filled or fully incinerated. This doesn’t make any sense. We set out to fix this, to make this linear chain more circular and harmonious with nature,” says Ahmed.
After graduating from college and three long years spent on R&D, they developed cycoraⓇ – a regenerated alternative to conventional polyester that can be recycled and used many times: “We take end-of-life textile materials that would otherwise have been landfilled or incinerated into a molecular recycling process,” Ahmed says.
"A major challenge in this field is that polyester is usually blended with other fibers like cotton, rayon, and nylon," explains David Schiraldi, Professor of Organic Chemistry and Macromolecular Science at Case Western University, "to recycle the polyester into new textiles, a difficult and complete separation is required. With significant technical effort, Ambercycle has accomplished the separation of polyester from other fibers without causing the chemical degradation of the polyester.
“Recycling has been largely off limits in the textile industry for the past several generations, as there have always been quality concerns. Ambercycle has demonstrated that these issues can be overcome.”
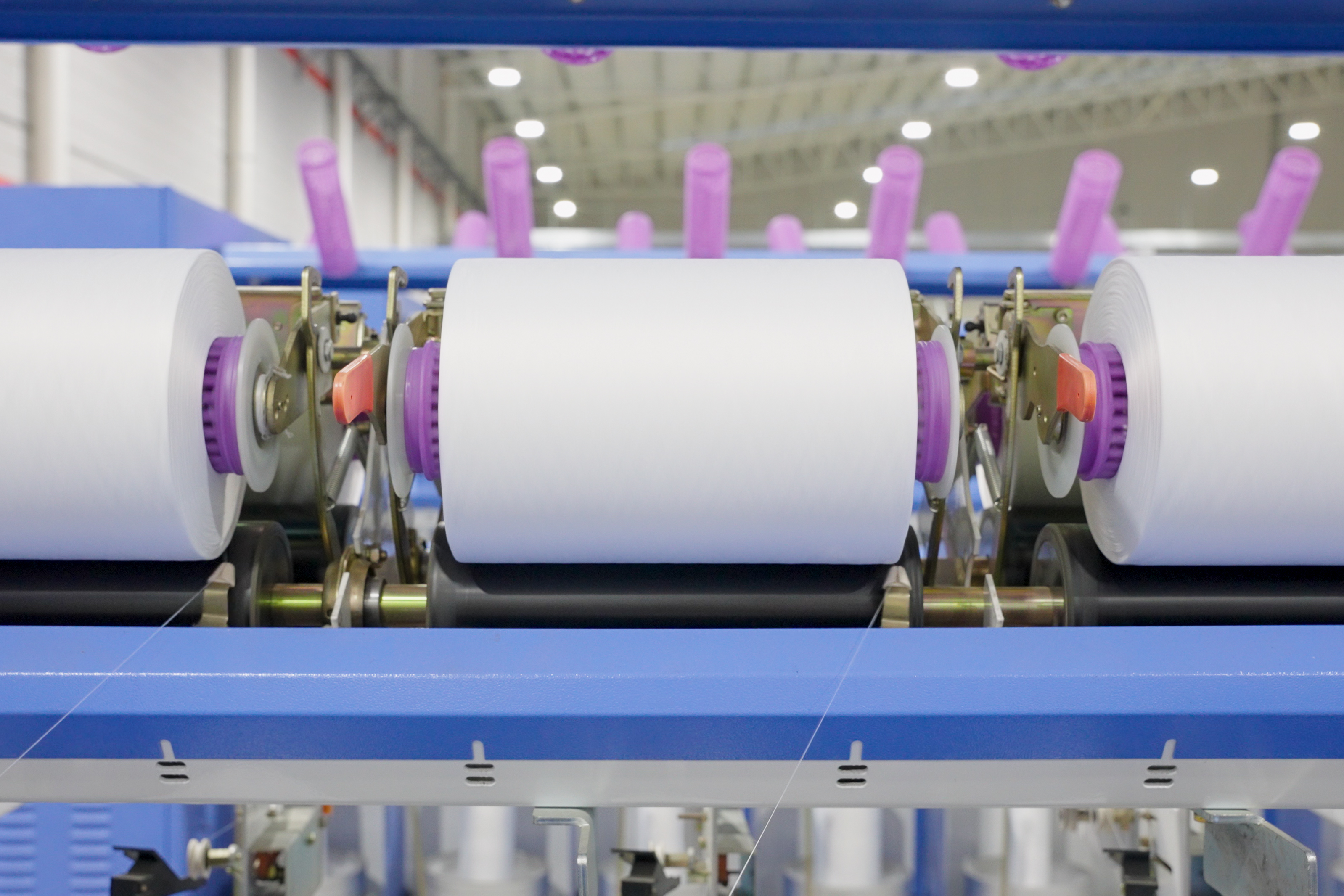
The fashion industry has taken note: Ambercycle has attracted investment and partnerships from some of the biggest name clothing brands, H&M, CO:LAB, and Zalando and raised $27 million in funding to build a circular textile ecosystem.
To date Ambercycle has diverted 3.5 million pounds of end-of-life textile waste away from landfill: "Over the past 8 years," says Sethi, "we’ve developed the technology and proved that the product works in capsule collections. The next step, crucial for the entire industry, is to adopt these solutions at scale. Manufacturing at that scale is a very different challenge than manufacturing with the lab bench scale we started with.”
Today Ambercycle is gearing up to create systemic change across the textile production and recycling sector, but in 2015, Sethi and Ahmed had started small: a 3-foot lab bench in northern California in the basement of an old biotech company became their research lab at the start of a relentless and often scrappy journey: “we had no experience, we’d just graduated,” says Sethi. “We were focused on getting to that next milestone; instead of using a 100-gallon reactor, we used a giant cooking pot. We did things that enabled us to spend less.”
“One formative experience was when a piece of equipment was being offloaded from the truck, the pallet ripped, and this beautiful reactor we needed for our process just fell on the ground and shattered everywhere,” adds Ahmed.
With no money to replace the lost equipment, the 22-year-olds went to a restaurant supply store and pieced together a makeshift solution: “Whatever we could get our hands on to create one t-shirt from another t-shirt, that’s what we did,” says Ahmed.
“We had some donated equipment, a lot of guidance and mentorship, but there were many long nights on our 3-foot lab bench where we were trying every possible way to recycle textiles. Just making the first t-shirt out of an old t-shirt took three years, and it wasn’t very comfortable!”
The first t-shirt they successfully recycled is now proudly hanging on a wall in a museum in the Netherlands.
.webp)
“Over time, we talked to people and started to communicate our vision. Over the past five years, we’ve been extremely fortunate to attract more significant capital. Today, we’ve raised $27 million,” says Sethi.
Global VP of Innovation at Wolverine, Barry McGeough, says Sethi had introduced him to Ambercycle's chemical recycling methods at a conference "it was a 'first of its kind' that addressed the problem of apparel waste that the industry was just beginning to admit and address. They presented what was a holy grail solution... I have been working to accelerate the success of this technology ever since.”
McGeough initiated an innovation partnership between outdoor apparel brand Saucony and Ambercycle, “Within a single seasons' timeline they were able to produce fiber and high-performance fabric that was 25% post-consumer recycled, giving Saucony apparel the edge it needed to be an industry leader in sustainable and circular apparel and a path, together with Ambercycle, to get to 100%.”
Over the next 10-15 years, Ambercycle plans to build largescale recycling factories and create incentives to put garments into collection systems that will feed back directly into fabric supply chains.
“Success for us means attracting all of these materials towards us so we can reprocess and put them back in rather than having anything leaving that circle,” says Ahmed, “we’re creating a structure whereby polyester does not exit the supply chain.”
Source: https://www.forbes.com/sites/mariannelehnis/2023/08/24/from-campus-to-catwalk-the-college-graduates-behind-the-breakthrough-solution-to-fast-fashions-waste-problem/?sh=38f1c1f75862